Pedal to the Metal: Why California can’t ban gasoline-powered cars
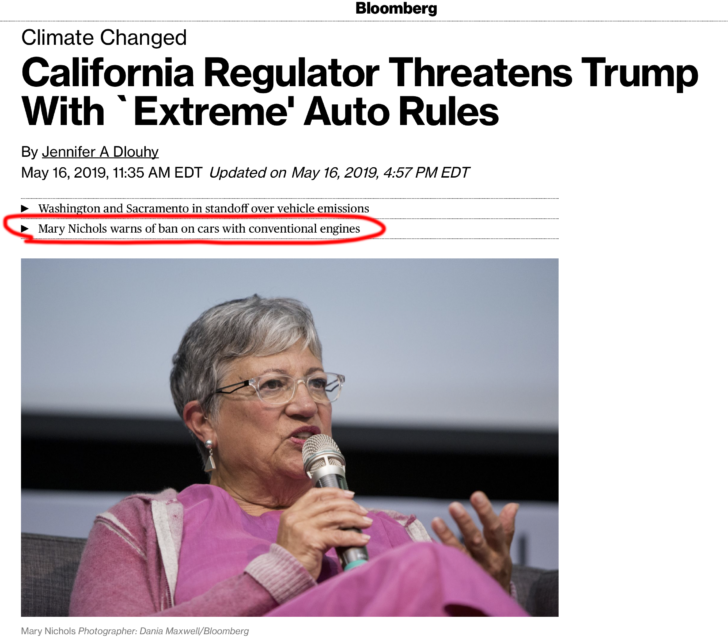
We report you decide.
This media release (Web | PDF) reports on a letter delivered by UK metals experts to the UK government’s Committee on Climate Change.
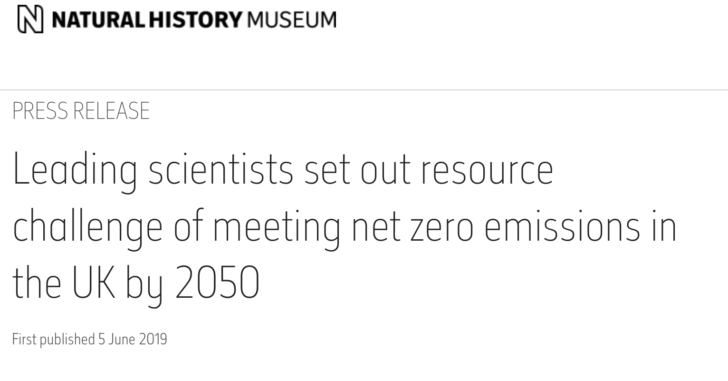
It sets out the energy and metal requirements to replace UK gasoline-powered cars with EVs:
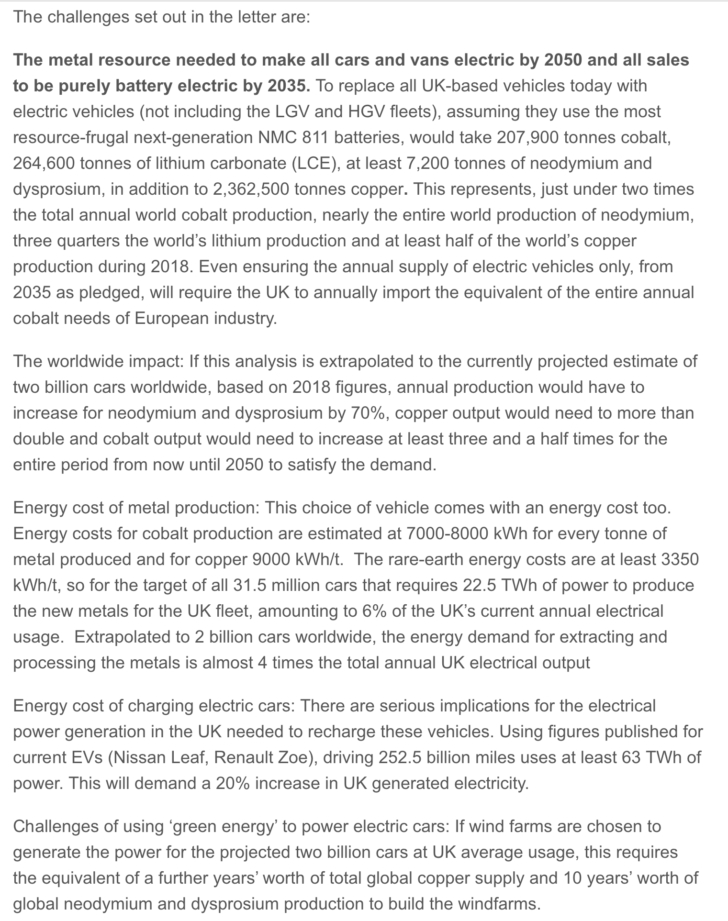
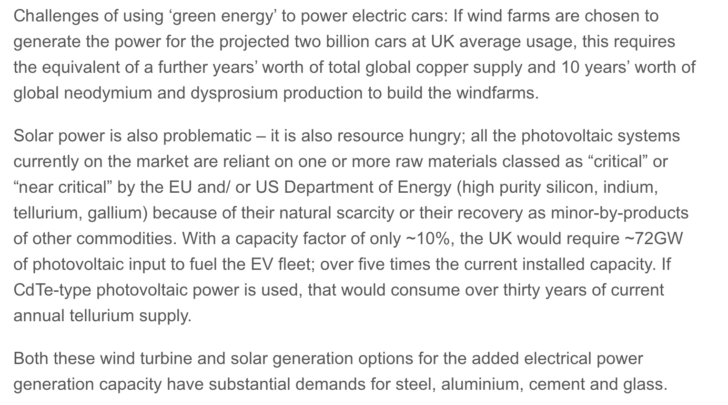
This translates to California as follows. As of 2018:
- The UK has about 38.2 million cars.
- California has about 25.6 million cars.
Replacing gasoline-powered cars with EVS in California would then require:
- 134% of current global cobalt production
- 67% of current global neodymium production
- 50% of current global production of lithium
- 34% of current global production of copper.
Not possible.
###
PRESS RELEASE
Leading scientists set out resource challenge of meeting net zero emissions in the UK by 2050
First published 5 June 2019
A letter authored by Natural History Museum Head of Earth Sciences Prof Richard Herrington and fellow expert members of SoS MinErals (an interdisciplinary programme of NERC-EPSRC-Newton-FAPESP funded research) has today been delivered to the Committee on Climate Change
The letter explains that to meet UK electric car targets for 2050 we would need to produce just under two times the current total annual world cobalt production, nearly the entire world production of neodymium, three quarters the world’s lithium production and at least half of the world’s copper production.
A 20% increase in UK-generated electricity would be required to charge the current 252.5 billion miles to be driven by UK cars.
Last month, the Committee on Climate Change published a report ‘Net Zero: The UK’s Contribution to Stopping Global Warming’ which concluded that ‘net zero is necessary, feasible and cost effective.’ As a major scientific research institution and authority on the natural world, the Natural History Museum supports the pressing need for a major reduction in carbon emissions to address further catastrophic consequences of climate change. Using its scientific expertise and vast collection of geological specimens, the Museum is collaborating with leading researchers to identify resource and environmental implications of the transition to green energy technologies including electric cars.
A letter which outlines these challenges was delivered to Baroness Brown, who chairs the Adaption Sub-Committee of the Committee on Climate Change.
Prof Richard Herrington says: “The urgent need to cut CO2 emissions to secure the future of our planet is clear, but there are huge implications for our natural resources not only to produce green technologies like electric cars but keep them charged.
“Over the next few decades, global supply of raw materials must drastically change to accommodate not just the UK’s transformation to a low carbon economy, but the whole world’s. Our role as scientists is to provide the evidence for how best to move towards a zero-carbon economy – society needs to understand that there is a raw material cost of going green and that both new research and investment is urgently needed for us to evaluate new ways to source these. This may include potentially considering sources much closer to where the metals are to be used.”
The challenges set out in the letter are:
The metal resource needed to make all cars and vans electric by 2050 and all sales to be purely battery electric by 2035. To replace all UK-based vehicles today with electric vehicles (not including the LGV and HGV fleets), assuming they use the most resource-frugal next-generation NMC 811 batteries, would take 207,900 tonnes cobalt, 264,600 tonnes of lithium carbonate (LCE), at least 7,200 tonnes of neodymium and dysprosium, in addition to 2,362,500 tonnes copper. This represents, just under two times the total annual world cobalt production, nearly the entire world production of neodymium, three quarters the world’s lithium production and at least half of the world’s copper production during 2018. Even ensuring the annual supply of electric vehicles only, from 2035 as pledged, will require the UK to annually import the equivalent of the entire annual cobalt needs of European industry.
The worldwide impact: If this analysis is extrapolated to the currently projected estimate of two billion cars worldwide, based on 2018 figures, annual production would have to increase for neodymium and dysprosium by 70%, copper output would need to more than double and cobalt output would need to increase at least three and a half times for the entire period from now until 2050 to satisfy the demand.
Energy cost of metal production: This choice of vehicle comes with an energy cost too. Energy costs for cobalt production are estimated at 7000-8000 kWh for every tonne of metal produced and for copper 9000 kWh/t. The rare-earth energy costs are at least 3350 kWh/t, so for the target of all 31.5 million cars that requires 22.5 TWh of power to produce the new metals for the UK fleet, amounting to 6% of the UK’s current annual electrical usage. Extrapolated to 2 billion cars worldwide, the energy demand for extracting and processing the metals is almost 4 times the total annual UK electrical output
Energy cost of charging electric cars: There are serious implications for the electrical power generation in the UK needed to recharge these vehicles. Using figures published for current EVs (Nissan Leaf, Renault Zoe), driving 252.5 billion miles uses at least 63 TWh of power. This will demand a 20% increase in UK generated electricity.
Challenges of using ‘green energy’ to power electric cars: If wind farms are chosen to generate the power for the projected two billion cars at UK average usage, this requires the equivalent of a further years’ worth of total global copper supply and 10 years’ worth of global neodymium and dysprosium production to build the windfarms.
Solar power is also problematic – it is also resource hungry; all the photovoltaic systems currently on the market are reliant on one or more raw materials classed as “critical” or “near critical” by the EU and/ or US Department of Energy (high purity silicon, indium, tellurium, gallium) because of their natural scarcity or their recovery as minor-by-products of other commodities. With a capacity factor of only ~10%, the UK would require ~72GW of photovoltaic input to fuel the EV fleet; over five times the current installed capacity. If CdTe-type photovoltaic power is used, that would consume over thirty years of current annual tellurium supply.
Both these wind turbine and solar generation options for the added electrical power generation capacity have substantial demands for steel, aluminium, cement and glass.
The co-signatories, like Prof Herrington are part of SoS MinErals, an interdisciplinary programme of NERC-EPSRC-Newton-FAPESP funded research focusing on the science needed to sustain the security of supply of strategic minerals in a changing environment. This programme falls under NERC’s sustainable use of natural resources (SUNR) strategic theme. They are:
Professor Adrian Boyce, Professor of Applied Geology at The Scottish Universities Environmental Research Centre
Paul Lusty, Team Leader for Ore Deposits and Commodities at British Geological Survey
Dr Bramley Murton, Associate Head of Marine Geosciences at the National Oceanography Centre
Dr Jonathan Naden, Science Coordination Team Lead of NERC SoS MinErals Programme, British Geological Society
Professor Stephen Roberts, Professor of Geology, School of Ocean and Earth Science, University of Southampton
Associate Professor Dan Smith, Applied and Environmental Geology, University of Leicester
Professor Frances Wall, Professor of Applied Mineralogy at Camborne School of Mines, University of Exeter
No comments:
Post a Comment